The Coupling Elements of the Production Workflow at DELL
DELL implements the Just-in-Time (JIT) or “build-to-order” model which facilitates the coordination of different production processes and increases supply chain flexibility (Songini, 2000, par. 2).
The company uses the information technology (IT) system that allows it to integrate different organizational workflows including engineering, operations, service delivery, and sales (Rouse & Sage, 2007), and automate resource planning and, in this way, increases the accuracy of forecasting and scheduling.
DELL’s IT system integrates customer service operations, material requirements planning (MRT), capacity requirements planning (CRT), material supply, and product distribution.
IT-supported MRT and CRT are critical to the organization of manufacturing process as these planning functions allow the prediction of potential shortages, the monitoring of material flows and material status; they also support the selection of appropriate machinery, assembly, facilities, etc. (Rouse & Sage, 2007).
DELL employs an Internet-based supply chain management system which allows the company to notify the suppliers about the required components and helps to shorten the time of delivery (Songini, 2000).
DELL’s Manufacturing Workflow Chart
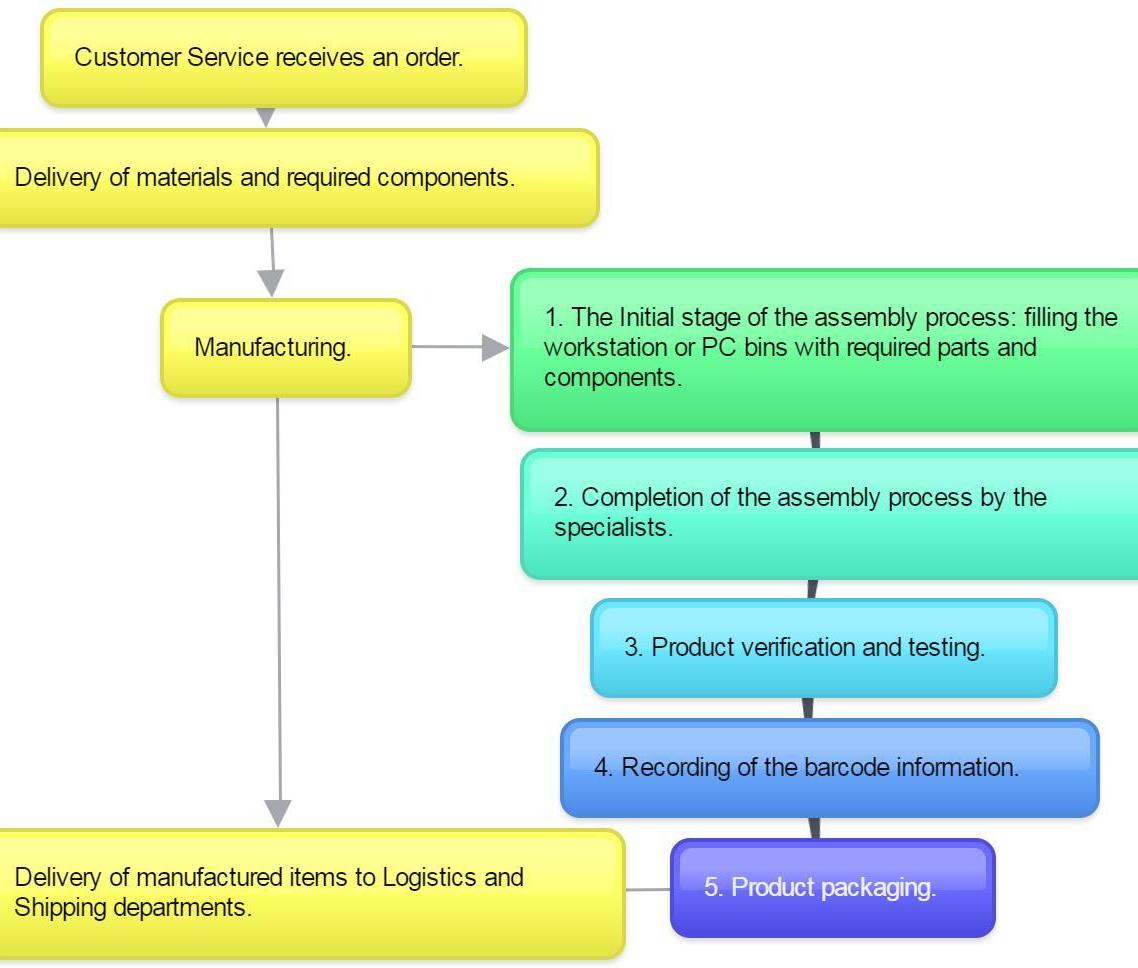
Workflow Justification
The use of automated equipment and skilled labor allows the workers to complete the assembly of an item within five minutes (Kanellos, 2004). In this way, DELL achieves significant time and energy efficiency.
By following JIT principles, DELL does not store any material at its facilities and brings in the exact number of components ordered by a customer (Kanellos, 2004). Therefore, the inventory costs are eliminated.
The short-term production schedule is run daily at DELL. It helps the company “to maintain accuracy and to stabilize production levels” for the minimization of potential production expenditures and flaws (Rouse & Sage, 2007).
Layout Efficiency and Effectiveness
DELL’s production model reflects the consideration of employee resource count, process efficiency, consumer volume, adequate selection of practices and systems. By addressing each operational component at every production phase, the company becomes able to control and maintain high operational velocity which is one of the major criteria of production efficiency.
The organizational operations and production tasks are designed according to the JIT principles which are associated with advantages such as the decrease in storage expenses, the reduction of production cycle due to the decrease in batch size; as well as the rationalization of production process through the supplier specialization and accurate delivery time scheduling (Green et al. 2014).
Currently, DELL strives to produce over 2350 items per hour (Kanellos, 2004). And it is possible to assume that such a high level of effectiveness is supported by the efficient management the resources.
The processes and workflows integrated into the production model allow DELL to consider the needs of its legitimate stakeholders (customers, suppliers, and shareholders) and provide added values (e.g. short production cycle and quick product delivery) for them. By creating benefits for its stakeholders, the company gains an opportunity to maintain a high level of profitability, customer loyalty, and good reputation that will support sustainable business performance (Santana, 2011).
The Issues of Client Convenience
The major DELL’s clients are the retailers who usually order and purchase large volumes of products to sell them at their facilities and stores. Thus, their major concern with the company’s production workflows is the velocity and safety of manufacturing and delivery.
The automated and IT-based workflow design suits the flexible production, and logistics approach that implies “little penalty of time, effort, cost, or performance” (Jafari, 2015, p. 947). It means that the sequence of processes administered at DELL may have lesser negative impacts on organizational performance regarding damage and repair costs, service expenditures, and risks to impede corporate reputation due to manufacturing and delivery delays and customers’ discontent.
DELL’ workflow provides the retailers with an opportunity to receive their orders and start sales faster.
Safety, Environment, Ergonomics
As it is stated at the official company’s website, “Dell products are designed and tested to meet the appropriate worldwide standards for Product Safety, Electromagnetic Compatibility, Ergonomics and other regulatory compulsory requirements, when used for their intended purpose” (Regulatory compliance policy, 2016, par. 1).
The products’ high level of energy efficiency benefits the environment and allows the consumers to reduce costs for power consumption (Worldwide regulatory compliance engineering and environmental affairs, 2014).
In its production processes, DELL complies with E-Waste regulations that imply the reduced use of hazardous materials (Worldwide regulatory compliance engineering and environmental affairs, 2014). In order to enforce the safety regulations, DELL controls its internal designs and planning, introduces supplier declarations, thoroughly analyzes the technical documentation and tests the supplied materials.
The company uses recyclable materials for both product manufacturing and packaging.
DELL designs its products in a way that allows consumers to gain significant advantages from the use of the products (Product safety, EMC and environmental datasheets, 2016). Throughout the process of product development and manufacturing, the company focuses on the international technological and ergonomics standards which facilitate the production of the advanced computers and aim to improve the interactions between people and machines.
References
Rouse, W. B., & Sage, A. P. (2007). Work, workflow and information systems. Amsterdam, the Netherlands: IOS Press.
Green, K., Inman, R., Birou, L., & Whitten, D. (2014). Total JIT (T-JIT) and its impact on supply chain competency and organizational performance. International Journal of Production Economics, 147, 125-135.
Santana, A. (2012). Three elements of stakeholder legitimacy. Journal of Business Ethics, 105(2), 257–265.
Jafari, H. (2015). Logistics flexibility: A systematic review. International Journal of Productivity and Performance Management,64(7), 947-970. doi:10.1108/ijppm-05-2014-0069
Regulatory compliance policy. (2016).
Worldwide regulatory compliance engineering and environmental affairs. (2014).
Product safety, EMC and environmental datasheets. (2016).
Songini, M. (2000). Just-in-Time manufacturing. Computerworld.
Kanellos, M. (2004). Inside Dell’s manufacturing mecca. CNET.